Mechanical Measurements and Interventions
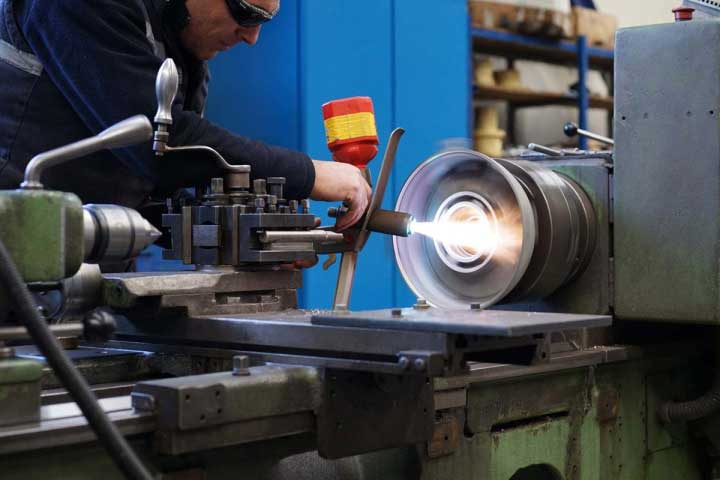
Mechanical issues account for a significant portion of spindle motor failures. According to statistics, approximately 65% of electric motor failures worldwide are attributed to mechanical problems. Due to the production pressures on machines where spindle motors are used, they are often not given adequate downtime for regular and periodic maintenance. This lack of maintenance contributes to serious mechanical problems and subsequent motor failures.
If these mechanical issues are not identified in a timely manner, they can lead to:
- Damage to the bearing housings in the front and rear motor covers
- Damage to the motor bearings
- Damage to the front and rear bearing housings of the rotor shaft
- Damage to the keyway in the rotor shaft
- Damage to the coupling and pulley locations on the rotor shaft
Failure to address these mechanical problems promptly and adequately can significantly prolong and increase the cost of repair and maintenance processes.
Changing the bearings of spindle motors requires extra attention. Due to the high operating speeds, the material properties, cage structures, and lubrication types of the bearings used may vary. It is crucial to use the same type and specifications of bearings. The tightness tolerances of the bearing housings should be measured with precision, and if any issues are detected, they must be meticulously addressed.
Our company has an advanced technical infrastructure that enables us to efficiently and effectively resolve all mechanical problems. Additionally, with our in-house lathe workshop equipped with turning machines and Castolin Thermal Spray technology, our skilled technical personnel can coat and process the rotor shaft bearing housings, as well as the motor cover bearing housings. This enables us to expedite the repair and maintenance processes and provide our customers with fast and guaranteed service in a cost-effective manner.